Обработка металлов давлением. Технологии и машины обработки давлением. Рубрика в журнале - Вестник Южно-Уральского государственного университета. Серия: Металлургия
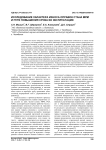
Исследование характера износа оправок стана МРМ и пути повышения срока их эксплуатации
Статья научная
Проведен анализ оборудования, указаны основные конструктивные особенности и описан состав оправочного узла непрерывного стана МРМ (Multistand Pipe Mill). На основе анализа литературных источников исследованы условия эксплуатации и наиболее характерные виды износа. Охарактеризован режим работы и описаны причины выхода из строя оправок. Указана проблематика стойкости инструмента. Показана необходимость рациональности подхода к расчету длины оправок. Рассмотрены особенности расчета длины оправки при непрерывной прокатке труб и приведены значимые неучитываемые факторы, такие как кратность проката, расстояние между непрерывным и извлекательно-калибровочным станами, расположение наиболее изнашиваемого участка, режимы деформации, которые, в конечном счете, влияют на ресурс работы оправочного узла и другого оборудования. На основе опытных данных рассмотрены особенности износа оправочного узла непрерывного стана МРМ. Приведен анализ влияния различных факторов на эксплуатационную стойкость рабочей части оправок. Рассмотрены существующие пути повышения ресурса работы инструмента. Выданы рекомендации с целью увеличения стойкости прокатного инструмента. Определены основные перспективные направления для повышения срока эксплуатации оправочного узла, установленного на заводе непрерывного стана МРМ.
Бесплатно
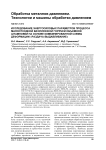
Статья научная
В данной работе представлено продолжение темы по разработке технологии малоотходной безуклонной горячей объемной штамповки осесимметричных деталей, в частности воротниковых фланцев, на основе схемы деформации «раздача-выдавливание». В настоящей статье приведен вывод общего вида функции энергосиловых параметров процесса на основе предыдущих работ, заключающихся в определении граничных условий и определения кинематических характеристик операции. Исходя из условий и схемы процесса деформации, принимаем торовую систему координат. Вывод общего вида функции осуществлен по методике А.Л. Воронцова. Так как процесс осесимметричный, то рассматриваем плоское напряженное состояние очага деформации. Приведенная математическая модель разработана с целью верхней оценки усилия деформации, что связано с необходимостью проведения технологических расчетов на производстве. Также в данной работе представлено моделирование по новой схеме деформирования с целью качественной оценки пластического течения материала. По результатам моделирования подтверждена практическая применимость метода на практике, что подтверждает предыдущие предположения. Также рассмотрен график зависимости усилия штамповки от перемещения. В данном конкретном случае график имеет куполообразную форму, что обусловлено изменением площади контакта рабочего инструмента с заготовкой. С целью получения более достоверной картины процесса деформации проведен лабораторный эксперимент на базе лаборатории кафедры ПиМОМД на гидравлической установке ВЖМ-2М, материал - свинец марки С2С ГОСТ 3778-98. Гидравлическая установка ВЖМ-2М отличается удобством применения и приемлемым усилием. Данный эксперимент дал положительные результаты, подтвердив тем самым моделирование при помощи метода конечных элементов. Для полноценной проверки корректности математической модели планируется проведение неполнофакторного эксперимента. Разработан пакет конструкторской и технологической документации, на данном этапе проекта оснастка находится на изготовлении в НОЦ «Машиностроение». Также планируется освоение опытной партии фланцев на ООО «ЧТЗ-УралТрак» на типоразмере с диаметром условного прохода D50.
Бесплатно
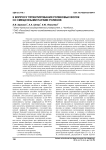
К вопросу проектирования роликовых волок со смещенными парами роликов
Статья научная
Показана тенденция развития производства проволоки фасонного и круглого сечения из различных металлов и сплавов. По данным анализа существующих конструкций и оборудования, используемых при производстве проволоки, выявлены факторы, влияющие на качество продукции. Из них выделены факторы, играющие большую роль при производстве проволоки мелких сечений, а именно: жесткость конструкции волоки, точность настройки калибров стана, устойчивость полосы в калибре. Подробно исследовано влияние последнего фактора при эксплуатации роликовых волок со смещенными парами роликов. Для данных конструкций роликовых волок получена зависимость определения минимально возможного расстояния между осями пар роликов. Показано влияние величины обжатия и диаметра готового профиля на величину этого расстояния. Разработана методика определения максимально возможного расстояния между осями пар роликов, исходя из условия потери устойчивости полосы во втором калибре при использовании системы калибров «круг - овал - круг». Представлены основные этапы методики, а именно определение следующих параметров: усилия действующего на металл заготовки со стороны роликов, горизонтальной проекции площади очага деформации, сваливающего момента, действующего на заготовку, предельного угла скручивания заготовки, максимальной длины заготовки между очагами деформации. Показано влияние на рассчитанную величину максимального расстояния между осями пар роликов величины обжатия. Описаны сферы применения полученных зависимостей. Представлена и описана конструкция разработанной роликовой волоки, спроектированной с учетом теоретических выкладок, представленных в данной статье. Конструкция роликовой волоки отличается возможностью использования модульной сборки и упрощенной схемой регулировки.
Бесплатно
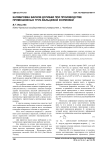
Калибровка валков догибки при производстве прямошовных труб вальцевой формовки
Статья научная
Качество стыковых швов при монтаже магистральных газопроводов, а значит и показатели их эксплуатационной надежности в значительной мере зависят от степени отклонения поперечного сечения труб от окружности, особенно в их торцевых частях. Современные регламенты качества трубной продукции для транспортировки углеводородов, особенно для трубопроводов с подводными переходами, накладывают жесткие ограничения на отклонения профиля в поперечном сечении от окружности. Допуски в ряде случаев по этому показателю не превышают 3…5 мм, что соответствует 0,45…0,8 % от диаметра труб. В практике производства прямошовных труб в линии RBE-LSAW с использованием для догибки валков фирмы HAEUSLER не удается стабильно обеспечить качество геометрии зон догибки. Разработана методика калибровки валков клети догибки прикромочных участков заготовки для труб большого диаметра, которая обеспечивает монотонный, без локальных отклонений от геометрии окружности, переход зоны догибки к основному периметру, сформованному предварительно на вальцевой листогибочной машине.
Бесплатно
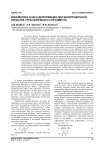
Кинематика очага деформации при безоправочной прокатке труб нефтяного сортамента
Статья научная
Рассмотрен процесс безоправочной прокатки труб нефтяного сортамента. Получены зависимости определения параметров калибровки относительно известных обжатия и величины овализации калибра. Обосновано создание математической модели процесса редуцирования и работы извлекательно-калибровочного стана. Приведены зависимости определения основных параметров очага деформации. Получены системы уравнений для нахождения поверхности контакта металла трубной заготовки и инструмента для двухвалкового и трехвалкового калибров. Представлено поле скоростей металла трубной заготовки. Из условия, что осевая компонента вектора скорости изменяется по квадратичному закону и скорость металла на входе очаг деформации со скоростью выхода из очага деформации связаны коэффициентом вытяжки, получена зависимость для определения этой компоненты вектора скорости. Обоснован линейный закон распределения радиальной компоненты вектора скорости металла трубной заготовки, из условия связи осевой компоненты вектора скорости и радиальной тангенсом угла между рассматриваемым сечением и вертикальной плоскостью симметрии валка получена зависимость для определения радиальной составляющей вектора скорости. Третья компонента вектора скорости определена из условия несжимаемости, которое определено для трехвалкового и двухвалкового калибра. На основе определенных компонент вектора скорости определены компоненты тензора скоростей деформации для трехвалкового и двухвалкового калибров. Компоненты тензора скоростей деформации рассчитаны для случая прокатки труб на редукционном трехвалковом стане. Произведена численная оценка компонент тензора скоростей деформации, определены компоненты тензора скоростей деформации, которые возможно не учитывать при проведении инженерных расчетов с использование тензора скоростей деформации.
Бесплатно
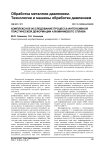
Комплексное исследование процесса интенсивной пластической деформации алюминиевого сплава
Статья научная
На сегодняшний день существует множество способов интенсивного пластического деформирования (ИПД) металлов. Часть из них изучена в достаточной мере, другая - только начинает входить в круг интересов исследователей. У каждого из них есть положительные и отрицательные черты. При этом все они без исключения имеют ряд особенностей, в том числе формирование высокодефектной структуры металла. Отслеживание течения металла и образования различных дефектов на стадии подготовки к физическому эксперименту позволяет предупредить возможное появление некоторых из них, что положительно сказывается на качестве полученных образцов. В работе приведены результаты математического моделирования с помощью программного продукта Deform с оценкой формирования дефектов макроструктуры в течение всего процесса получения заготовки. Проведен анализ течения металла с целью определения причин возникновения дефектов. Для подтверждения корректности построенной модели приведены результаты натурного эксперимента, полностью соответствующего моделируемому. Анализ полученных результатов говорит о высокой сходимости результатов математического моделирования и физического эксперимента, что подтверждает возможность использования программных продуктов в качестве инструмента научных исследований.
Бесплатно
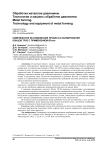
Комплексное исследование процесса калибрования концов труб с применением QFORM
Статья научная
В настоящее время с каждым годом происходит значительный рост требований к точности геометрических параметров труб. Одним из важных показателей является овальность концов труб, для обеспечения которой в ТПЦ-3 АО «ВТЗ» имеется оборудование для калибрования. Одними из самых сложных по исполнению являются спецификации на магистральные трубы из углеродистой стали. В указанных спецификациях прописаны самые важные требования к внутреннему диаметру, овальности концов труб, локальной овальности, толщине стенки. Данные трубы с ужесточением к внутреннему овалу достаточно востребованы на Ближнем Востоке и Северной Африке, однако из-за невозможности выполнить предъявляемые требования заказчика приходилось отказываться от большого количества заказов. Поэтому в данной статье рассмотрены условия работы калибрования концов труб с помощью наружного и внутреннего формоизменения. Выделены основные проблемы, при которых не удавалось достичь требуемых параметров (повышенной овальности на концах труб). С помощью программного продукта QForm 2D/3D проведено компьютерное моделирование с варьированием процесса калибрования с различными калибровками инструмента. Из полученных результатов моделирования выделены параметры, по величине которых можно судить о склонности инструмента к разрушению и налипанию на металл: усилия, действующие на рабочую поверхность колец в процессе калибрования; площадь пятна контакта (износ инструментов). На основе результатов разработана новая калибровка колец как для наружного, так и для внутреннего калибрования. Были проведены практические испытания колец с различной калибровкой, а именно различными углами входного/выходного конусов.
Бесплатно

Статья научная
Сталь с перлитной структурой является классическим примером наноструктурированного материала. Холоднотянутая высокоуглеродистая сталь с перлитной микроструктурой является сырьем для современных армирующих канатов. Главными свойствообразующими процессами в ходе волочения такой стали являются изменения межпластиночного расстояния и металлографической структуры, а также переориентация зёрен. Однако экспериментальное исследование динамики данных процессов является затруднительным и трудоемким. Исследован процесс девятикратного волочения стальной проволоки с перлитной структурой. На основе мультимасштабных компьютерных моделей было изучено поведение перлитных колоний на поверхности и центральном слое проволоки. В качестве программного решения был использован коммерческий комплекс Abaqus. Ключевыми факторами были ориентации цементитных пластин относительно оси волочения, межпластиночное расстояние и форма цементитных включений. На основе конечно-элементных моделей установлены закономерности переориентации перлитных колоний, изменения формы и размеров цементитных пластин и локализации деформации в феррите. Установлено, что цементитные пластины, которые были параллельными оси волочения, испытывают максимальное утонение и изменение межпластиночного расстояния. Пластины цементита, которые были перпендикулярны оси волочения, наиболее подвержены разрушению. Однако установлено, что при определенных значениях межпластиночного расстояния этот эффект может снижаться. В случае расположения перлитной колонии под углом к оси волочения наблюдалась их интенсивная переориентация относительно оси волочения. При этом наблюдались значительный изгиб цементитных пластин и их подверженность фрагментации. На основании моделирования установлены функциональные зависимости межпластиночного расстояния и утонения пластин цементита от степени деформации. Произведено сравнение расчетного значения механических свойств проволоки с реальным экспериментом. Результаты моделей были верифицированы посредством металлографических исследований.
Бесплатно
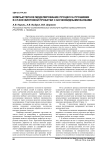
Компьютерное моделирование процесса прошивки в стане винтовой прокатки с бочковидными валками
Статья научная
Представлены результаты компьютерного моделирования процесса винтовой прошивки заготовки на стане с бочковидными валками и неподвижными направляющими линейками. Компьютерное моделирование производилось в программе QForm 3D, основанной на методе конечных элементов. Моделирование процесса винтовой прокатки позволило объяснить характер изменения напряженно-деформированного состояния центральной зоны металла при прокатке на двухвалковом прошивном стане за один полный оборот заготовки и объяснить разрушения в центральной зоне заготовки, являющейся основной причиной появления внутренних плен на гильзах и трубах. Разрушение центральной зоны заготовки происходит из-за действия осевых растягивающих напряжений. В результате компьютерного моделирования определено влияние оправки на характер напряженно-деформированного состояния центральной зоны заготовки. Наличие оправки резко снижает уровень растягивающих напряжений в центральной зоне заготовки по причине подпирающих сил, что в практике трубного производства приводит к увеличению прошиваемости заготовки и уменьшает или «заваривает» вскрытие осевой зоны металла. В данной работе также определено влияние коэффициента овализации и угла подачи на уровень осевых растягивающих напряжений в центральной зоне заготовки. Увеличение угла подачи увеличивает как растягивающие напряжения в заготовке, так и сжимающие перед торцем оправки. Поэтому необходимо процесс прошивки вести при условии, чтобы заготовка делала меньше одного оборота до встречи с торцом оправки, но не меньше 3/4 оборота, иначе возникнут проблемы с вторичным захватом. С увеличением коэффициента овализации увеличиваются растягивающие напряжения в центральной зоне заготовки. Полученные результаты моделирования соответствуют основным положениям теории обработки металлов давлением. Высокая достоверность результатов компьютерного моделирования позволяет осуществлять проверку разработанных калибровок прокатного инструмента и скоростных режимов без проведения дорогостоящих опытных прокаток.
Бесплатно
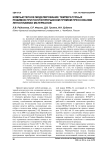
Статья научная
При холодном прямом прессовании легкоплавких материалов разогрев металла и оснастки, вызванный деформационными процессами и контактным трением, является причиной снижения качества готовой продукции и потерей стабильности процесса. АО «Челябинский цинковый завод» совместно с кафедрой «Процессы и машины обработки металлов давлением» ЮУрГУ с 2019 года активно и успешно занимается разработкой и освоением технологии производства проволочного и пруткового припоя из сплава ПОИн-52. В настоящей работе, используя специализированный инженерный пакет QForm, провели компьютерное моделирование температурных режимов процесса прессования проволочного припоя из сплава ПОИн-52 диаметром 2,0 мм со скоростью прессования 0,5; 1,0 и 3,0 мм/с из заготовки диаметром 20 мм. По результатам компьютерного моделирования установлено, что скорость истечения металла из волоки, которая в свою очередь определяется скоростью прессования и коэффициентом вытяжки, оказывает существенное влияние на температурные условия процесса прессования. При изменении скорости прессования с 0,5 до 3 мм/с в процессе прессования проволоки Ø2,0 мм из заготовки Ø20 мм температура металла возрастает с 33,4 до 75,8 °С. Причем стоит отметить, что последовательное прессование четырех заготовок приводит к повышению температуры проволоки с 75,8 до 87 °С. Связано это с тем, что в процессе непрерывного прессования оснастка, а именно волока, разогревается и уже после четвертого цикла прессования ее средняя температура составляет около 45 °С. Средняя температура контейнера повышается при этом на 4 °С. После четвертого цикла дальнейшее повышение температуры как прессуемого металла, так и проволоки на исследуемом диаметре припоя прекращается и процесс стабилизируется.
Бесплатно
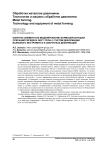
Статья научная
Работа посвящена исследованию формообразующих операций, применяемых в производстве труб большого диаметра (ТБД) с использованием трехвалковой листогибочной машины (вальцев). В программном комплексе Marc.Mentat разработаны конечно-элементные модели процессов вальцевой формовки, догибки кромок, сборки, сварки и экспандирования трубы. Объектом исследования является труба диаметром 1420 мм с толщиной стенки 21,6 мм и длиной 12 м из стали группы прочности X70. В модели трубы использовались тонкостенные (Shell) элементы, что позволяло относительно быстро осуществлять процесс моделирования без существенной потери точности расчетов. Проведено комплексное конечно-элементное моделирование формообразующих операций передела лист-труба с учетом деформации верхнего валка листогибочной машины и сварочных деформаций. Установлено, что при каждой технологической операции в трубе возникает неоднородное напряженно-деформированное состояние (НДС), которое оказывает влияние на конечную геометрию труб. Показано, что наибольшую неоднородность НДС в трубу вносят вальцевая формовка и догибка кромок. Разработанная комплексная конечно-элементная модель может быть использована исследователями и технологами для расчета настроек технологического оборудования и энергосиловых параметров формообразующих операций.
Бесплатно
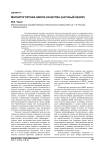
Магнитогорская школа качества (научный обзор)
Статья научная
Систематизированы основные достижения научно-педагогической школы по управлению качеством продукции и производственных процессов в металлургии Магнитогорского государственного технического университета им. Г.И. Носова. В цепочке технологического процесса металлургического производства продукции присутствует достаточно большой спектр технических операций и задача разработки методов выбора рационального технологического процесса на основе комбинирования различных операций ОМД является актуальной. Закономерным этапом исследования и решения таких задач стало открытие при Магнитогорском государственном техническом университете им. Г.И. Носова диссертационного совета Д 212.111.05 по специальности 05.02.23 - Стандартизация и управление качеством продукции. Интегрируя исследования в сфере квалиметрии, менеджмента качества и совершенствования технологий, этот совет в России является единственным в области черной металлургии по развитию научных направлений: совершенствование связей взаимодействия системы «поставщик - разработчик - изготовитель»; научные основы стандартизации; квалиметрические методы оценки качества объектов и процессов управления качеством; методы анализа, синтеза и оптимизации, информационные модели состояния и динамики качества объектов. Все основные научные исследования магнитогорских ученых нашли применение на ведущих металлургических и машиностроительных предприятиях страны.
Бесплатно
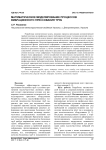
Математическое моделирование процессов вибрационного прессования труб
Статья научная
Разработана математическая модель динамики процесса прессования осесимметричной трубной заготовки на профильном прессе трубопрессовой линии. Согласно расчетной схеме и принятой динамической модели процесса прессования трубной заготовки получены аналитические выражения для соответствующих взаимодействующих границ пластической и упругой зон очага деформации. Получена аналитическая зависимость, характеризующая скорость распространения фронта пластической деформации в зависимости от скорости перемещения прессуемого металла. Определены динамические характеристики возникновения волновых явлений в прессуемом металле с учетом условий воздействия со стороны инструмента, что существенно дополняет ранее известные представления о напряженно-деформированном состоянии металла в очаге деформации. Установлены поля деформаций в зонах возмущенной области очага деформации с учетом воздействия технологических инструментов. Путем моделирования динамических процессов в прессуемом металле установлены особенности реализации высокоэффективной технологии управляемого вибрационного прессования труб на профильном прессе трубопрессовой линии. Выбором рациональных параметров (амплитудно-частотной характеристики) используемого активного процесса вибрационного прессования трубной заготовки достигнуто значительное повышение эффективности процесса и качества прошиваемых заготовок.
Бесплатно
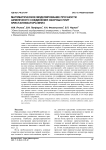
Математическое моделирование прочности шпилечного соединения сборных плит кристаллизатора МНЛЗ
Статья научная
Наиболее ответственным узлом при разливке стали в машине непрерывного литья заготовок является кристаллизатор. Наибольшее распространение получают удобные в эксплуатации и изготовлении составные кристаллизаторы, состоящие из медной рабочей стенки со щелевыми каналами и стального внешнего корпуса. В промышленных конструкциях составных кристаллизаторов соединение медной и стальной плит осуществляется посредством множества стальных шпилек, причем они расположены по поверхности плиты крайне неравномерно из-за наличия каналов охлаждения, шпонок и уплотнителя. Целью работы является создание математической модели для определения коэффициента неравномерности нагружения шпилек и запаса прочности соединения медной и стальной плит для заданной конструкции сборного кристаллизатора и выбранных типовых параметров шпилечного соединения. Учет возникающих неодинаковых нагрузок на шпильки осуществлялся путем расчета коэффициента неравномерности. Полагали, что максимальная растягивающая сила, приходящаяся на одну шпильку, пропорциональна этому коэффициенту и средней растягивающей силе. Для каждой шпильки выделялся кластер, включающий в себя заданное число ближайших к ней шпилек. Определялось среднее расстояние в кластере, среднее значение расстояния по всем кластерам и относительное расстояние для кластера, связанного с определенной шпилькой. Нагрузка на резьбовое соединение пропорциональна площади соединяемых плит, которые удерживает шпилька, поэтому полагали, что коэффициент неравномерности нагрузки для заданной шпильки пропорционален квадрату относительного расстояния. Показан пример расчета коэффициента неравномерности нагрузки для рассматриваемой конструкции промышленного сборного кристаллизатора. Приведена математическая модель для определения запаса прочности шпилечного соединения медной и стальной плит кристаллизатора, а также необходимого момента затяжки шпильки, обеспечивающего нераскрытие стыка. Расчеты учитывали максимальное испытательное давление воды и максимальное внешнее усилие сдвига при трении слитка о стенку кристаллизатора. Создана компьютерная программа, позволяющая анализировать надежность соединения стальной и медной стенки кристаллизатора машины непрерывного литья заготовок при моделировании разных ситуаций, в том числе форс-мажорных и аварийных.
Бесплатно
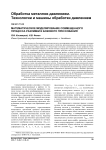
Математическое моделирование совмещенного процесса разливки и бокового прессования
Статья научная
Представлена и обоснована цель математического моделирования совмещенного процесса разливки и бокового прессования с применением нового устройства, предназначенного для реализации на вертикальном прессовом оборудовании, что обеспечивает получение длинномерных полых профилей. Показаны основные параметры процесса, действия которых определяют структуру моделируемой системы, свойства ее элементов и причинно-следственные связи, присущие системе и существенные для достижения цели моделирования. Для упрощенного описания процесс условно разделен на две зависимые стадии, определяемые объемом металла в контейнере. Выполнен учет характерных, влияющих на условия и результаты прессования, зон, в которых металл на рассматриваемой стадии в истечении практически не участвует и образует объемы пластически не деформирующегося, находящегося в упругом состоянии металла. Разработана математическая модель определения энергосиловых параметров процесса, с учетом воздействия аккумулирующего устройства, что позволяет определять в том числе значения требуемого усилия для выпрессовки пресс-остатка. Очевидным преимуществом математической модели для определения усилия при получении труб способом совмещения процесса разливки и бокового прессования, является возможность сравнительно быстрого сопоставления результатов при разных режимах процесса. Выполнено численное исследование совмещенного процесса разливки и бокового прессования для различных марок сталей. Проведено сравнение результатов численного исследования процесса с использованием математической модели и результатов, полученных и использованием программного продукта для моделирования и оптимизации процессов ОМД QForm 2D/3D. Обоснована необходимость проведения дальнейших исследований процесса с использованием физической модели.
Бесплатно
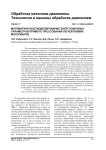
Математическое моделирование энергосиловых параметров прямого прессования легкоплавких материалов
Статья научная
При прессовании легкоплавких материалов крайне важным является определение технологических параметров процесса. В настоящей работе разработана математическая модель прямого прессования проволоки и прутков из легкоплавких материалов, позволяющая определить энергосиловые параметры процесса. Проверку адекватности математической модели осуществляли в ходе лабораторного эксперимента на гидравлическом прессе. В лабораторных условиях измерялись и фиксировались усилие и скорость прессования с помощью установленной на нем системы сбора данных. Проверка адекватности проводилась при прессовании прутков ø8,00 и 15 мм и проволоки ø2,00 мм и показала высокую сходимость расчетов с экспериментальными замерами. Ошибка не превышала 10 %. Полученная математическая модель была использована для аналитических исследований технологических режимов прямого прессования прутков и проволоки из сплава ПОИн-52. Расчеты показали, что уменьшение диаметра готового прутка (проволоки) с 16,00 до 2,00 мм при сохранении размера заготовки ø30,00 мм приводит к увеличению усилия прессования с 86 кН до 131 кН в начальный момент прессования, так как существенно с 4 до 256 возрастает коэффициент вытяжки. Усилие при прессовании прутка ø8,00 мм с увеличением диаметра заготовки с 12,0 до 40,0 мм возрастает с 25 до 171 кН. Проведение аналитических исследований на модели показало, что возможно не только изучать процесс прессования с целью понимания механизмов формирования механических и эксплуатационных свойств готового прутка (проволоки), но и проектировать ресурсосберегающие режимы прессования для различного сортамента продукции, осуществлять обоснованный выбор требуемого оборудования и оснастки.
Бесплатно
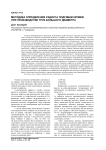
Методика определения радиуса подгибки кромок при производстве труб большого диаметра
Статья научная
Системы трубопроводного транспорта, включающие трубы большого диаметра как неотъемлемую часть, относятся к опасным техногенным объектам. Их аварии или отказы в работе приводят к возникновению серьезных угроз населению, инженерным сооружениям и природным массивам. Поэтому к ним предъявляются высокие требования по обеспечению надежности и безопасности. Текущее развитие производства электросварных труб большого диаметра напрямую зависит от требований, предъявляемых компаниями топливно-энергетического комплекса. Из-за истощения традиционных месторождений и стремления к расширению рынков сбыта компании топливно-энергетического комплекса вынуждены переходить к добыче и транспортировке углеводородов в новых условиях. Развитие новых проектов таких, как «Сила Сибири», предполагает прокладку трубопроводов в зонах тектонической активности, что также повышает требования к надежности труб. Одним из направлений развития производства электросварных труб большого диаметра является повышение группы прочности. Увеличение надежности и экономичности электросварных труб большого диаметра достигается не только повышением механических свойств трубных сталей путем их легирования, но и повышением геометрических требований к сварным трубам. При производстве труб большого диаметра основными геометрическими требованиями являются: отклонение наружного диаметра труб, овальность и отклонение от теоретической окружности. Нарушение в технологии производства влечет появление дефектов на трубах. Геометрические дефекты в трубах закладываются в заготовках. Одним из основных геометрических дефектов при производстве труб является отклонение от теоретической окружности. Исправление данного дефекта осуществляется операцией калибрования на механическом экспандере. Отклонение от теоретической окружности происходит из-за неправильного выбора радиуса прикромочной зоны при подгибке кромок на прессе. Предложен способ расчета и определения радиуса подгибки кромки после распружинения.
Бесплатно
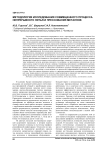
Методология исследования совмещенного процесса непрерывного литья и прессования металлов
Статья научная
Рассмотрены схемы совмещения непрерывного литья с прессованием алюминиевых сплавов: Конформ, Экстроллинг, Линекс, совмещенная прокатка-прессование. Показано, что методология расчета основных технологических параметров совмещенного процесса литья-прессования алюминиевых сплавов с использованием карусельного кристаллизатора должна включать нахождение рациональных размеров поперечного сечения контейнера, определение величины входного угла матрицы, расчет значения угла между каналом матрицы и продольной осью контейнера, определение длины контейнера, определение места заливки расплава в канавку колеса кристаллизатора в зависимости от заданных значений температуры, скорости прессования, интенсивности охлаждения рабочего инструмента при стабильном процессе деформирования. Для нахождения зависимости времени остывания от перечисленных факторов применялось планирование экспериментов типа 24 и получено уравнение регрессии. По результатам теоретических расчетов была спроектирована и изготовлена опытная установка совмещенного литья и прессования цветных металлов, на которой были проведены эксперименты по установлению влияния на процесс кристаллизации остывания и последующего прессования заготовок из алюминиевых сплавов, температуры поверхности канавки колеса-кристаллизатора, площади ее поперечного сечения, температуры заливаемого металла, величины заходного угла матрицы и ее расположение относительно дна канавки колеса, скорости подачи металла к матрице, температуры прессования и коэффициента вытяжки. Было установлено, что совмещение процессов непрерывного литья и прессования в одном инструменте должно обеспечивать создание и соблюдение постоянного градиента температуры металла на участке его заливки в кристаллизатор и в зоне матрицы, где происходит деформирование кристаллизованной заготовки. При этом уровень градиента зависит от характера распределения температуры вдоль переходной зоны твердо-жидкого состояния металла в кристаллизаторе и определяет как энергосиловые параметры процесса деформирования, так и качество получаемого пресс-изделия.
Бесплатно
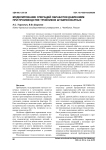
Моделирование операций обработки давлением при производстве тройников штампосварных
Статья научная
Существует несколько основных технологий изготовления тройников. Данные технологии различаются по способу выполнения формоизменяющих операций и применяемому оборудованию. Выбор параметров для каждой технологической операции напрямую определяет качество готовой продукции. При этом расчёт технологических параметров инженерными методиками представляется затруднительным. Поэтому целесообразным является применение современных программ для моделирования технологических операций. Рассматривается моделирование технологических операций обработки металлов давлением в программе DEFORM, применяемых в различных технологиях производства тройников. Заготовка и инструмент для моделирования технологических операций были созданы в программе SolidWorks. В программе DEFORM были последовательно промоделированы операции частичного охлаждения нагретой заготовки, набора металла в зону отбортовки и операция отбортовки. По результатам моделирования были определены технологические параметры, по которым в дальнейшем была произведена опытная штамповка деталей «тройник». Замер параметров готовых изделий показал, что результаты расчета оказались очень близки к результатам опытной штамповки. Сходимость результатов варьировалась для разных технологий в диапазоне от 95 до 99 %. Определены основные факторы, влияющие на сходимость результатов моделирования и опытной штамповки. Полученные тройники признаны годными, полностью удовлетворяющими требованиям технических условий. Таким образом, показано, что применение программного комплекса DEFORM на предприятиях, производящих штампосварные детали трубопровода, целесообразно и позволит сократить срок ввода в производство нового изделия.
Бесплатно
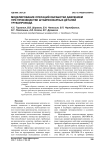
Моделирование операций обработки давлением при производстве штампосварных деталей трубопровода
Статья научная
При производстве тройников заготовка подвергается ряду технологических операций, в том числе нагреву, частичному охлаждению и обработке давлением. Выбор параметров для каждой технологической операции напрямую определяет качество готовой продукции. При этом расчёт технологических параметров инженерными методиками представляется затруднительным. Поэтому целесообразным является применение современных программ для моделирования технологических операций. Рассматривается моделирование технологических операций обработки металлов давлением в программе DEFORM. Заготовка и инструмент для моделирования технологических операций были созданы в программе SolidWorks. В программе DEFORM были последовательно промоделированы операции частичного охлаждения нагретой заготовки, набора металла в зону отбортовки и операция отбортовки. На первом этапе моделировалось частичное охлаждение заготовки путём помещения её в ванну на глубину 2/3 от её высоты и выдержки в течение заданного временного интервала. Затем было проведено моделирование операции набора металла в зону отбортовки, при этом была определена оптимальная высота выпуклости. На третьем этапе была промоделирована операция вырезки отверстия под отбортовку, в ходе которого были определены размеры отверстия. На последнем этапе была промоделирована отбортовка ответвления, после чего было определено соответствие толщины стенки ответвления полученной на модели техническим требованиям на изделие. По результатам моделирования были определены технологические параметры, по которым в дальнейшем была произведена опытная штамповка детали «тройник». Замер параметров готового изделия показал, что результаты расчета оказались очень близки к результатам опытной штамповки, а полученный тройник признан годным, полностью удовлетворяющим требованиям технических условий. Таким образом, показано, что применение программного комплекса DEFORM на предприятиях, производящих штампосварные детали трубопровода, целесообразно и позволит сократить срок ввода в производство нового изделия.
Бесплатно